Sandblasting Romford
Sandblasting London are a sand blaster in Romford and Greater London. We provide a variety of shot blasting services using many different abrasive blasting materials. Contact our mobile sandblasters now to enquire about our services!
Sand Blaster in Romford
Welcome to Sandblasting London, your go-to provider for high-quality sandblasting services in Romford. We are experts in providing high-quality sandblasting services for residential, commercial, and industrial clients.
Sandblasting London is a leading local sandblasting company based in the vibrant city of London. With years of experience and a team of skilled professionals, we specialise in providing high-quality sandblasting services for a wide range of industries and applications. Our expertise lies in effectively removing rust, old paint, and surface contaminants from various materials, including metal, concrete, glass, and stone. We pride ourselves on delivering exceptional results through the use of advanced sandblasting equipment and techniques. Search for “sandblasting near me” and do not hesitate to call us!
Give us a call today!
Get A Free Instant Quote!
London Sandblasting leads
3500+
Jobs Completed!
2800+
Delighted Customers!
20+
Years of Experience!
Why Choose Sandblasting London?
Versatile
Every job is different and requires a unique approach. That's why we offer many sandblasting services that can be adapted to suit your specific needs, whether you require paint removal, rust removal from metal, or surface preparation.
Experience
Our sand blasters have years of experience in the industry and have worked on hundreds of projects, from large-scale industrial sandblasting and commercial sandblasting to smaller residential projects. We have the expertise to carry out any job and can recommend the best blasting material for a given job.
Customer Service
At Sandblasting London, we put our customers first. We take pride in our approachable and professional service. We understand that communication is critical, and we will keep you informed throughout the entire process. We are always happy to answer any queries or concerns you may have and can offer guidance as to the best technique to use for your specific project.
Affordable Prices
We think that sandblasting should be a viable option for everybody, which is why we offer competitive pricing on all our services. We always strive to keep affordable rates without compromising on the quality of our services.
Accuracy
Sandblasting London take great pride in delivering top-quality results that meet the high standards of our clients. We know that a lot of our customers jobs require extreme precision. This is why we only use the best equipment and techniques to ensure every job is completed to the highest level of satisfaction.
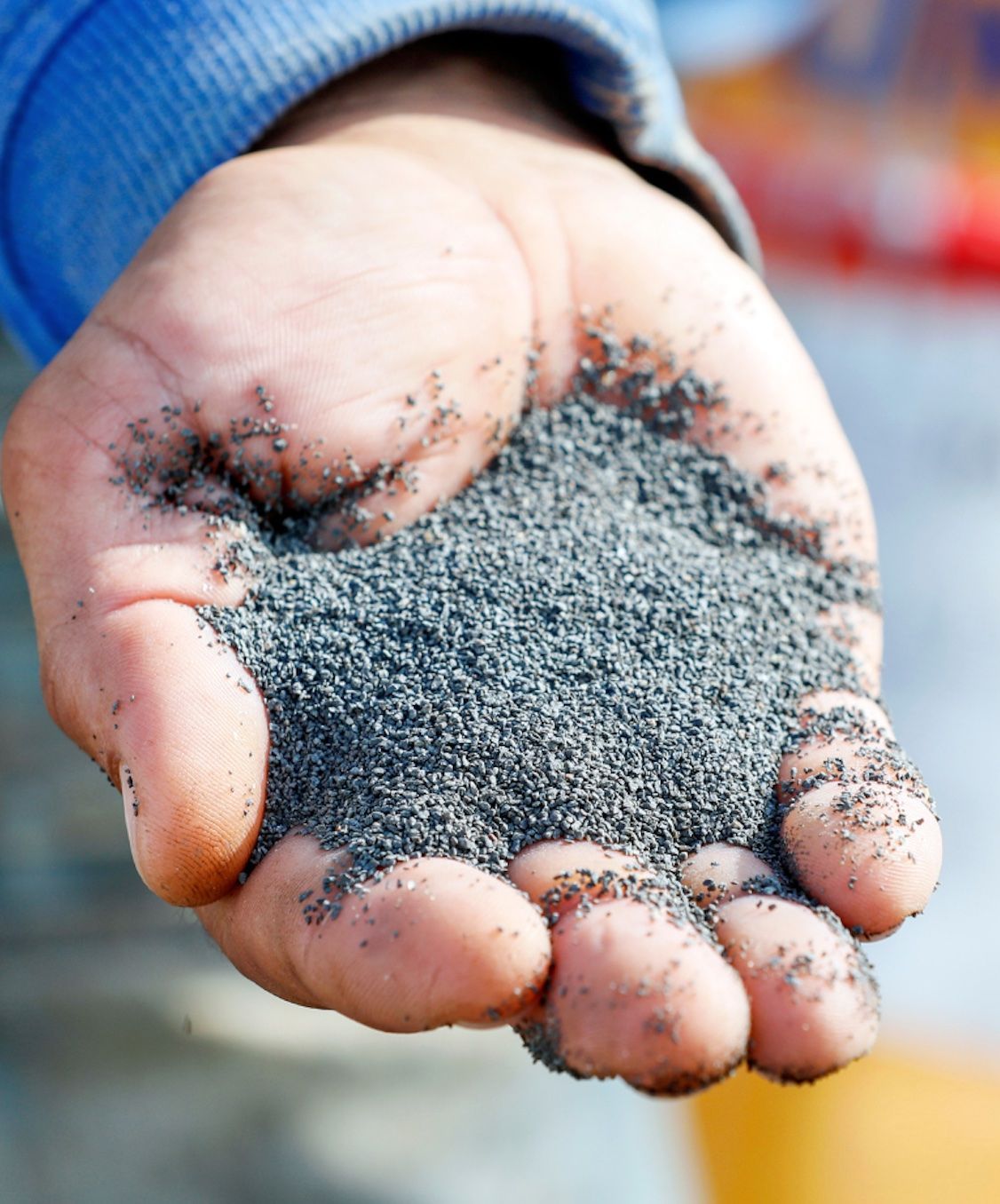
What Is Sandblasting?
Sandblasting, also known as abrasive blasting, is a technique used by sand blasters to clean, prepare, or etch surfaces by propelling fine particles at high speeds. It involves using compressed air or a specialised blasting machine to forcefully propel abrasive materials, such as sand, glass beads, or walnut shells, onto a surface.
We often provide
sandblasting in Romford on a variety of surfaces, such as
sandblasting stainless steel,
sandblasting vinyl, or to
sandblast wood. It serves multiple purposes, such as removing rust, paint, or coatings from metal, preparing surfaces for a painting or coating application, or to create a textured or etched finish on materials like glass or stone.
Sandblasting is a versatile technique used to clean and prepare by propelling abrasive particles at high speeds. The sandblasting process involves directing the abrasive material towards the surface being treated. The impact of the high speed particles effectively removes contaminants, debris, or unwanted coatings, leaving behind a clean and prepared surface. It is used in various industries and is an effective surface restoration and preparation method. Look for
local sandblasting services near you and start your sandblasting project and find
best sandblasters in your area.
What Does Sandblasting Do?
Sandblasting serves several purposes and can be used for various applications. Here are the primary functions of sandblasting:
Cleans Surfaces
Grit blasting effectively removes contaminants, dirt, rust, scale, old paint, or other unwanted substances from surfaces. It provides a thorough cleaning by forcefully propelling abrasive particles onto the surface, dislodging and stripping away unwanted materials.
Prepares Surfaces
Sandblasting prepares surfaces for further treatment or coatings. Removing old paint, rust, or corrosion creates a clean, textured surface that enhances adhesion for subsequent painting, coating, or bonding processes. Proper surface preparation ensures better durability and longevity of applied finishes.
Removes Coatings
Abrasive blasting is commonly employed to remove existing coatings, such as paint or varnish, from surfaces. The high-velocity impact of abrasive particles effectively strips away the old coating, preparing the surface for a new application or restoration.
Engraves and Textures
Sandblasting can be used to create decorative or functional surface patterns, textures, or designs. By selectively directing the abrasive particles, you can etch or engrave glass, stone, or metal surfaces, resulting in unique and visually appealing finishes.
Restores and Refurbs
Sandblasting is often utilised in restoration projects to revive and rejuvenate old or worn surfaces. It can help restore the original appearance of historic buildings, statues, or metal structures by removing years of accumulated grime, corrosion, or coatings.
Profiles Surfaces
Grit blasting can alter the surface profile of materials, particularly in commercial sandblasting. By adjusting the abrasive material and blasting settings, it is possible to create specific surface roughness or texture required for improved adhesion, grip, or friction.
Cleaning Welds
This type of blasting service is employed in the welding industry to clean weld joints and remove welding residues. It helps achieve cleaner welds and prepares surfaces for inspections or subsequent welding action.
What Is Sandblasting Used For?
Surface Preparation
Dry sandblasting or wet sandblasting is widely used for surface preparation before painting, coating, or bonding. It effectively removes rust, scale, old paint, and other contaminants, providing a clean and properly textured surface that improves the adhesion and durability of subsequent finishes.
Coating Removal
Sandblasting strips off existing coatings, such as paint, varnish, or powder coatings, from surfaces. It efficiently removes the old layers, allowing for reapplication or restoration of the surface.
Cleaning and Restoration
Sandblasting is utilised in cleaning and restoring various surfaces, including buildings, monuments, statues, and historical structures. It removes dirt, grime, pollutants, and years of weathering, revitalising the appearance of the surfaces.
Metal Surface Preparation
This technique is extensively used in the aerospace, manufacturing, and automotive industries. Preparing metal surfaces is required before welding, plating, or machining for example, shot blasting steel. It removes mill, rust, and other contaminants, ensuring the surface is prepared for the next coating.
Concrete Surface Preparation
Sandblasting prepares concrete surfaces for resurfacing or coatings. It roughens the surface, removes old layers, and promotes better adhesion of new materials, such as epoxy or concrete overlays.
Etching and Engraving
Sandblasting London use mobile dustless blasting for artistic and decorative purposes. It can create intricate patterns, designs, or text on glass, stone, or metal. Controlling the impact of the abrasive allows for precise etching or engraving, resulting in unique and visually appealing finishes.
Mould and Corrosion Removal
Sandblasting removes mould, corrosion, and surface imperfections from industrial equipment, machinery, and metal structures. It restores their integrity, extends their lifespan, and helps maintain optimal performance. Reach out to us for industrial sandblasting.
Surface Profiling
We employ sandblasting to achieve specific surface profiles required for improved bonding, adhesion, or friction. Some clients want roughness or texture on surfaces, which is beneficial for applications such as concrete pavements, anti-slip surfaces, or industrial flooring.
Monument and Memorial Cleaning
We regularly get ask to sandblast to clean and preserve monuments, memorials, and gravestones. It gently removes dirt, stains, and biological growth, rejuvenating these structures and maintaining their aesthetic appeal.
Why Do People Use Sandblasting?
People require sandblasting for several reasons due to its effectiveness and versatility. One main use is for surface preparation. Mobile sandblasting gives surfaces a thorough cleaning by removing rust, scale, old paint, and surface contaminants. This prepares the surface for painting, coating, or bonding. Additionally, sandblasting is needed for coating removal, stripping off existing layers of paint or varnish from surfaces. It restores worn or damaged surfaces by removing old coatings and preparing them for a new application.
A
wet blasting technique is also popular for cleaning and restoration purposes. It revitalises the appearance of buildings, statues, and historical structures by removing dirt, grime, pollutants, and years of weathering. It can bring an object back to its original beauty.
We often get asked for
shot blasting in Romford as it can be used across many industries and enabes professionals to achieve desired results efficiently and accurately. Simply search for “sandblaster near me” to look for
sandblasting companies who have skilled and
professional sandblasters.
What Are The Benefits Of Sandblasting?
Sandblasting offers several benefits across various industries and applications. Here are some key advantages of sandblasting:
Versatility
Shot blasting is a versatile process that can be used on various materials, including metal, concrete, glass, and stone. It can handle different surface sizes and shapes, making it suitable for construction, manufacturing, and automotive sandblasting.
Coating Removal
Our sand blaster is particularly effective in removing coatings, such as paint, varnish, or powder coatings. It saves time and effort compared to manual methods of coating removal.
Precise Etching and Engraving
Sandblasting allows for precise etching and engraving on materials like glass, stone, or metal. We can control the depth and design to make intricate and visually appealing patterns, logos, or text. This makes sandblasting a popular choice for artistic and decorative applications.
Surface Profiling
Abrasive blasting can alter the surface profile of materials, providing the desired roughness or texture required for improved adhesion, grip, or friction. This is beneficial in applications where surface characteristics play a huge role.
Cost-Effective
Our sandblasting services are more cost-effective than manual surface preparation or coating removal techniques. It saves in both time and labour, leading to increased efficiency and productivity. Moreover, properly preparing surfaces helps prevent premature coating failures, reducing the need for frequent maintenance or repeating the work.
Environmentally Friendly
With the shift towards safer abrasive materials, sandblasting has become more environmentally friendly. Using alternatives to sand, such as glass beads or walnut shells, reduces the release of harmful silica dust into the air, minimising health risks and environmental impact.
Types Of Grit Used For Sandblasting
Many different types of grit materials can be used for sandblasting, depending on the surface's nature and the finish required. Some of the main abrasive materials that we use to
sandblast on a daily basis are:
Crushed walnut shells
Crushed walnut shells offer an environmentally friendly alternative for sandblasting. This natural and biodegradable material is well-suited for cleaning and preparing surfaces like wood, fibreglass, and plastic. Their gentle yet effective abrasive properties allow for the removal of surface contaminants without causing damage to delicate surfaces. This type of grit is also utilised with a sandblaster for car restorations.
Aluminium oxide
Aluminium oxide is a widely used abrasive material due to its exceptional durability, making it highly effective in removing stubborn coatings or paint layers. It is particularly suited for challenging removal tasks. Additionally, aluminium oxide sandblasting can provide a fine finish on surfaces, making it the preferred option in many situations, including wheel sandblasting and metal sandblasting. Its versatility and reliability make it a valuable choice for achieving optimal results in the surface treatment processes.
Glass Beads
Glass beads are commonly chosen as a bead blasting material when dealing with delicate surfaces. These tiny glass beads offer a gentle abrasive action suitable for sandblasting wood or plastic. Their main applications involve surface cleaning and polishing, leaving a smooth and glossy finish. This type of grit can also be used in bead blasting stainless steel. Glass beads are useful for adding final touches and addressing minor surface imperfections in various projects.
Steel Grit
Steel grit, which comes from carbon steel, is a widely used by Sandblasting London for shot blasting applications. It is available in various sizes, from fine to rough and it removes rust and gets rid of other contaminants, ensuring a clean and smooth metal surface. Additionally, steel grit blasting proves its effectiveness by generating surface texture, which enhances the sticking capabilities for future coating applications.
Garnet
Garnet is another type of blasting material widely used across Romford for its exceptional hardness and durability. This makes it the preferred choice for dustless blasting. This natural mineral is commonly employed in tasks involving surface preparation, such as removing paint or coatings. Additionally, garnet is effective for sandblasting concrete.
What Is The Best Grit For Sandblasting?
The best grit depends on the surface you are blasting and the desired outcome. Here are some situations of when Sandblasting London would use the various types of abrasive materials:
- Rust Removal: When it comes to rust removal, coarse grit abrasives are typically preferred. Aluminium oxide, garnet, or crushed glass are popular choices for sandblasting metal surfaces. Coarse grits, such as 30 to 60 mesh, provide the necessary aggressiveness to strip away rust and corrosion.
- Aluminium Surface Preparation: For bead blasting aluminium surfaces, a finer grit is often recommended to avoid damaging the softer metal. Aluminium oxide, glass beads, or plastic media with grit sizes ranging from 80 to 120 mesh are commonly used. These finer grits provide a gentler blasting action while still achieving effective surface preparation.
- Paint Removal: Removing paint requires a balance between effective removal and minimising damage to the underlying surface. Medium to fine grit abrasives, such as aluminium oxide or crushed glass with grit sizes ranging from 80 to 120 mesh, are commonly used. These grits provide a controlled abrasive action for efficient paint removal without excessive surface roughness.
- Delicate Surfaces: Delicate surfaces like wood or fibreglass require a gentler blasting approach to avoid surface damage. The grit is used in conjunction with a sand blaster for wood restoration. Softer abrasives like baking soda, walnut shells, or plastic media are commonly used in such cases. These abrasives offer a softer impact and are less likely to cause surface etching or damage.
How Does Sandblasting Work?
Sandblasting propels abrasive materials at high speeds to forcefully impact and remove unwanted substances or prepare surfaces. Here's a step-by-step explanation of how the process typically works:
1. Preparation: The area or object to be sandblasted is prepared by cleaning it thoroughly and ensuring it is free from any loose debris or contaminants. Protective measures, such as covering nearby areas or masking specific parts, may be taken to avoid unintended blasting.
2.
Abrasive Material Selection: The appropriate abrasive material is chosen based on the desired outcome and the treated surface. Common abrasive materials include sand, glass beads, aluminium oxide, or garnet.
3.
Equipment Setup: A
mobile shot blasting machine or a
portable sandblaster is used to perform the sandblasting process.
Mobile blasting consists of a blasting nozzle, a pressure vessel to hold the abrasive material, and an air compressor or compressed air source to propel the particles.
4.
Pressurisation: The pressure vessel is filled with the selected abrasive material. Compressed air is then introduced into the system, pressuring the vessel and creating a force that propels the abrasive material through the blasting nozzle.
5. Blasting: The sand blaster aims the nozzle at the target surface and activates the blasting process by pulling a trigger. The compressed air propels the abrasive particles out of the nozzle at high velocity, hitting the surface being treated.
6.
Surface Impact: As the abrasive particles strike the surface, they effectively remove contaminants, rust, paint, or other unwanted substances. The force of impact and the type of abrasive material used determine the extent of material removal or surface preparation achieved.
7.
Control and Adjustments: Throughout the sandblasting process, the operator maintains control over the direction, speed, and intensity of the blasting. Adjustments may be made to the air pressure, nozzle distance, or abrasive flow rate to achieve the desired results without damaging the surface.
8.
Clean-up: Once the sandblasting process is complete, the treated surface is inspected to ensure it meets our high standards. Any remaining abrasive material or debris is cleaned or removed by either vacuuming, washing or repeating the process.
How Much Does It Cost To Sandblast In Romford?
The sandblasting cost in Romford can vary depending on several factors, including the size and complexity of the project, the type of surface being treated, the required preparation and finish, and the equipment and materials used. Additionally, different sandblasting service providers may have different sandblasting prices. Obtaining quotes from reputable sandblasting companies in Romford is best in order to get an accurate estimate for your specific project. As a rough estimate, the sandblasting cost per m2 typically ranges from £10 to £40 or more. However, it is important to note that this is a general estimate and the final cost may vary based on the specific project requirements and local market conditions.
For an accurate price for sandblasting in Romford, give our helpful team a call, we'd be happy to help.
Does Sandblasting Remove Rust?
Yes, abrasive sandblasting is an effective method for removing rust from metal surfaces. When rust forms on a metal, it creates a layer of corrosion that weakens the material and affects its appearance. Sandblasting can help restore the surface by forcefully propelling abrasive particles onto the rusted area. The high-velocity impact breaks down and removes the rust, leaving behind the clean underlying metal. It will look as good as new once our bead blasting is finished.
Abrasive blast cleaning is widely recognised as an efficient and reliable method for rust removal, making it a popular choice in industries such as automotive, construction, manufacturing, and restoration projects. The abrasive particles used in sandblasting, such as aluminium oxide, garnet, or crushed glass, have the necessary rigidity to remove rust effectively. The abrasive action of the particles removes the rust layer, exposing a clean and bare metal surface.
Sandblasting can reach crevices and corners, ensuring thorough rust removal from intricate or hard-to-reach areas.
Does Sandblasting Prevent Rust From Coming Back?
Sandblasting itself does not prevent rust from coming back. Sandblasting is primarily used to remove existing rust and prepare the surface for subsequent treatments that can help prevent rust formation in the future.
After
sandblasting, applying appropriate coatings or treatments to the surface is crucial to inhibit rust from reforming. These protective measures typically include applying a primer and a paint designed to resist corrosion. The chosen coating should be suitable for the type of metal being treated and the environmental conditions to which it will be exposed. The protective coating acts as a barrier, preventing moisture and oxygen from reaching the metal surface, which are the primary factors contributing to rust formation. It creates a layer of protection that helps to inhibit the corrosive process.
Sandblasting London are happy to provide advice on the best
primer to use for certain metals.
In addition to proper coatings, other preventive measures may include:
- Regular inspection and maintenance.
- Keeping the surface clean and dry.
- Addressing any areas of damage or scratches promptly.
Implementing these measures after shot blasting can significantly reduce the likelihood of rust recurrence and extend the lifespan of the treated surface.
Priming After Sandblasting
Priming is an essential step in the surface preparation process. Sandblasting removes rust, old paint, and contaminants from the surface, leaving it clean and ready for the application of a primer. Sandblasting and powder coating are two excellent surface restoring techniques that are perfect when used together.
Priming serves several purposes:
- Corrosion Protection: The primer acts as a protective layer between the metal surface and the environment. It creates a barrier that helps prevent moisture and oxygen from reaching the metal, reducing the risk of future rust formation.
- Adhesion Promotion: The primer enhances the adhesion of subsequent coatings, such as paint or topcoats, to the surface. It provides a stable and compatible base for the coat, ensuring better bonding and improved durability of the overall coating system.
- Surface Smoothing and Filling: Primers can help fill in minor imperfections or surface irregularities left after our
sand blaster has finished. This promotes a smoother finish and enhances the appearance of the final coating.
How Long After Sandblasting Should You Prime?
Our shot blasting services remove rust, contaminants, and old coatings from the surface, leaving it exposed and susceptible to oxidation. After we have finished, we recommend to prime the surface as soon as possible. The timing largely depends on the specific conditions and requirements of the project. However, it is generally best to prime the surface within 24 to 48 hours after sandblasting. Applying a primer promptly helps to protect the bare metal from moisture and oxygen, preventing the formation of new rust.
Priming right after
sandblasting ensures that the surface is clean and free from debris, allowing better adhesion of the primer to the surface. It also helps to prevent any potential flash rusting that may occur due to exposure to atmospheric conditions. If there is a delay in priming, it is crucial to keep the surface clean and dry. Any moisture, condensation, or environmental contaminants can hinder the adhesion and effectiveness of the primer. In such cases, it may be necessary to perform further surface cleaning or preparation before applying the primer.
People Regularly Ask...
Romford Neighbourhoods
If you want professional Sandblasting in Romford, then call our sandblasters. Get in touch today for a free quote!